How to Setup
Access Frame Scaffolding
Scaffolds should be erected by two or more people. One person should be knowledgeable in erecting scaffolding to supervise the work. These step-by-step instructions are only a general guide. You must always first follow the manufacturer’s and/or supplier’s specifications. The following examp le is based on building a scaffold that is 2.1 x 1.5 m (7 x 5 ft.) x 1 frame high.
Step 1
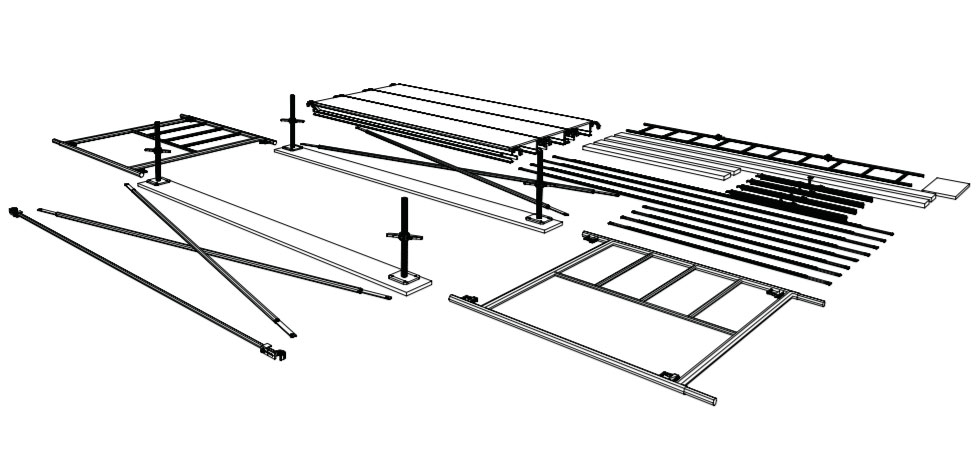
Select and prepare the ground area. Place suitable sills and make sure there are no holes under the sills. Select the equipment you need and place it near the work area. Put the adjustable base plates on the sills in the location that matches your scaffold dimensions. Do not secure the bases to the sills at this time.
Step 2
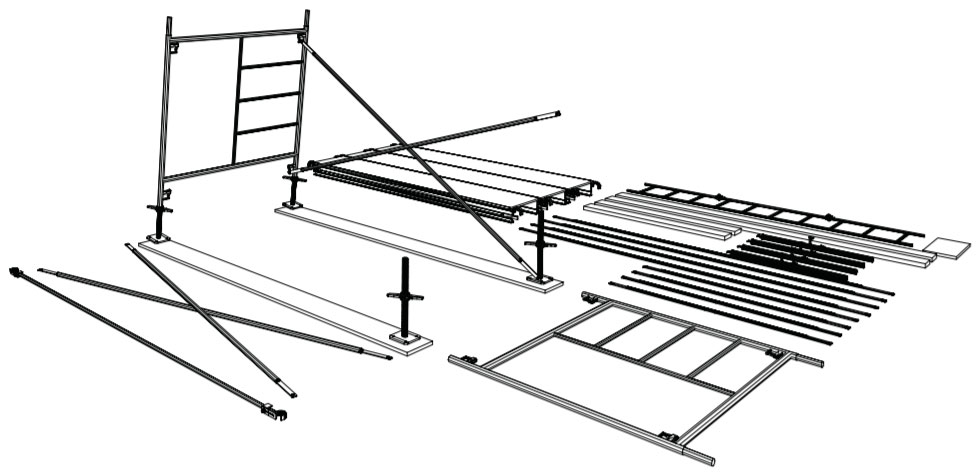
Adjust the base jack-nuts, starting at the highest point of the ground level. The jack-nut at the highest ground level should be set 7.5–15 cm (3–6 in.) from the top of the sill, depending on the slope. Place the first frame onto the base plates at the high point. Connect the first cross- brace to the frame. Allow the frame to lean slightly forward and rest on the sill while you prepare for the next frame to be installed.
Step 3
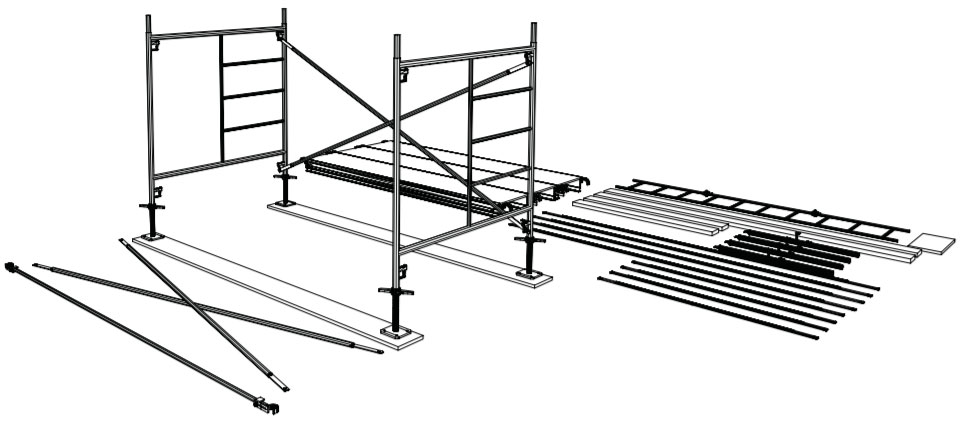
Install the second frame onto the base plates. Secure the first cross-brace to the second frame.
Step 4
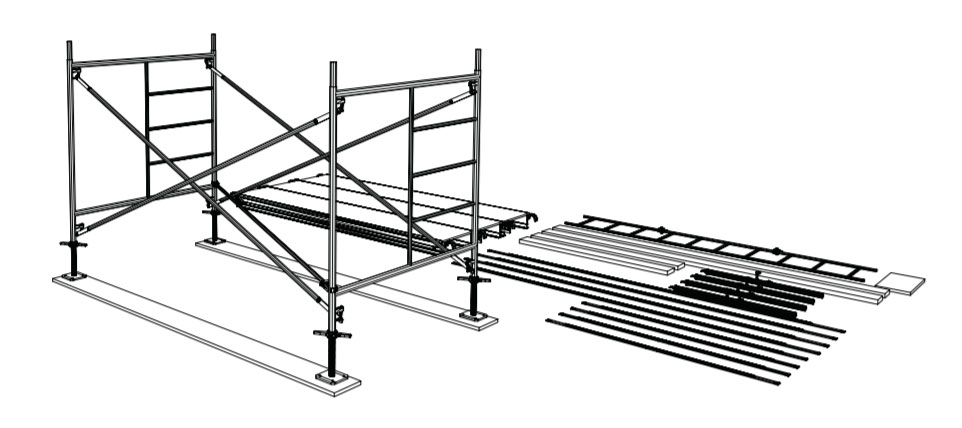
Install the second cross-brace to both the frames. Next you need to level and plumb the scaffold. Start at the high point of the scaffold. If possible, use the jack-nut to bring the highest corner down closer to the sill. Next bring all four corners up to that point. If the bottom cross-members of each frame are level with each other, the frames should also be plumb.
Install the plan brace (gooser bar) at this time to keep the scaffold square. Check the level again and plumb if necessary. Fasten the base plates to the sills with either nails or screws
Step 5
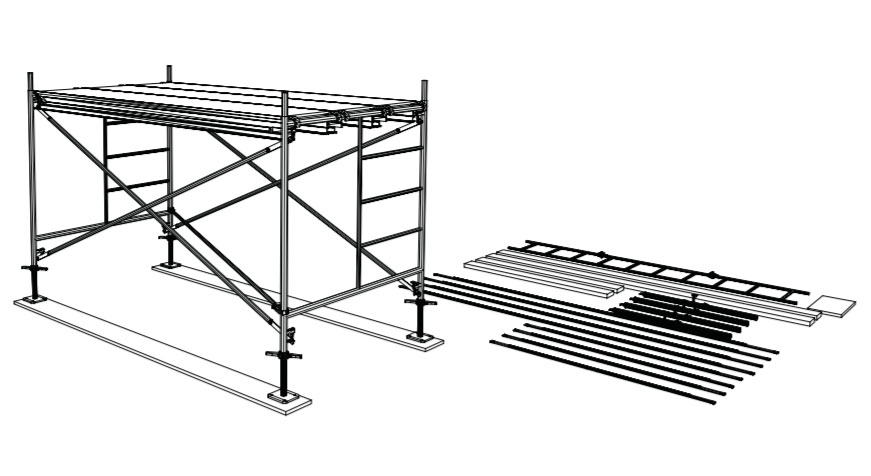
Install the decking, which may be metal or wood planks or the aluminum and plywood decking units. If you are using wooden planks, they must extend beyond the supporting cross-members at least 15 cm (6 in.) but not more than 30 cm (12 in.) Secure the decking so it cannot move.
Step 6
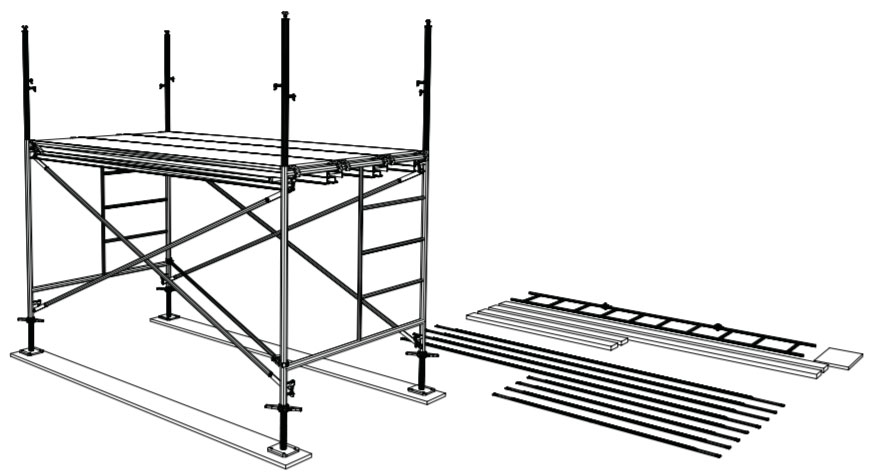
Select the equipment for the guardrail system. Purpose-made, wood, or tube and clamp could all be used. The following instructions are for purpose-made. Install the guardrail post onto the vertical coupling pins seated in the top of the frames. Put a lock pin through the top and bottom of each vertical coupling pin to avoid any separation.
Step 7
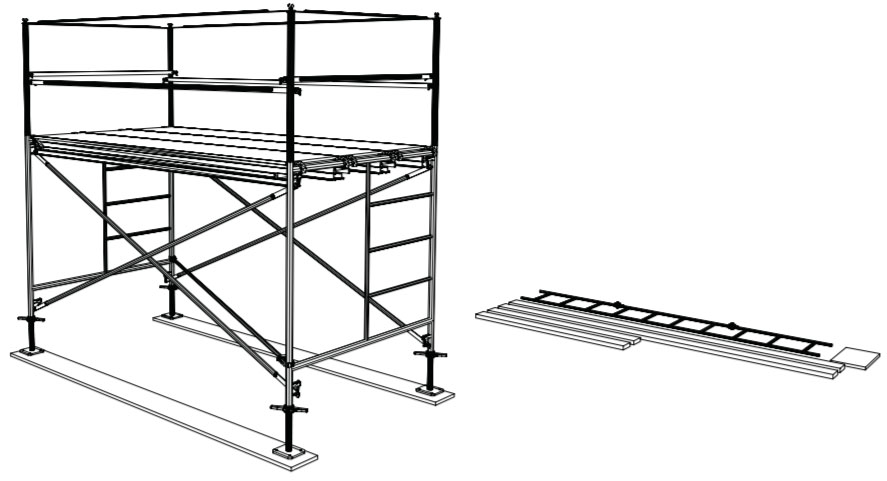
Attach the guardrails to the posts on all the exposed sides.
Step 8
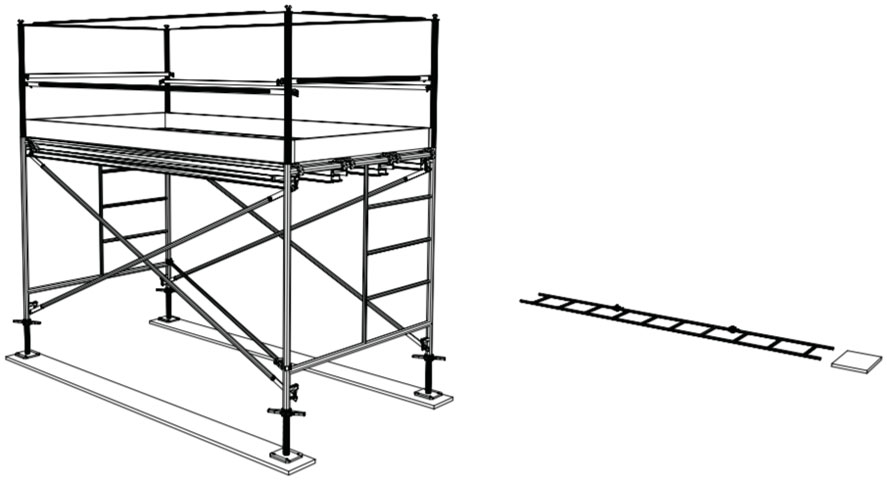
Install toeboards as required. The gap between the bottom of the toeboard and the top of the platform must not be more than 13 mm (1/2 in.).
Step 9
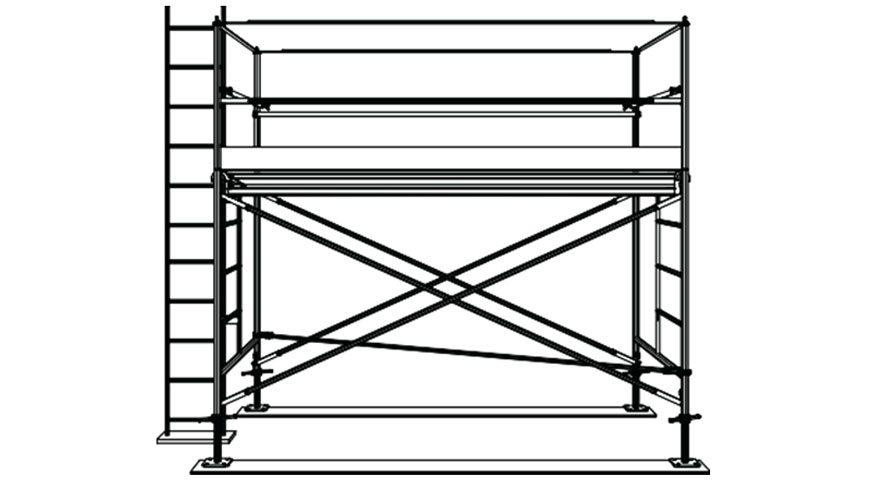
Install a suitable means of access, such as a sloping or vertical ladder secured to the scaffold at the landing point. The ladder must extend 1 m (3 ft.) above the landing.
Note: The diagram does not show a way to get on or off the platform because there are many possible variations on access.
Requirements for access frame scaffolding
- A scaffold must be erected, altered, and dismantled by qualified workers or under the direct supervision of a qualified person. The qualified person must ensure that the erection is carried out according to acceptable practices in compliance with any drawings and the manufacturer’s or supplier’s instructions, and that the correct components and materials are being
- All equipment must be inspected before use to ensure that it is in good repair and suitable for the intended
- The base must be firm and level enough to support the load of scaffolding, workers, and materials. Sills and base plates are required on any soil or unstable ground condition, or where any levelling adjustment is needed. The sill must be sound, rigid, and capable of supporting the maximum loads without settlement or
- Adjustable base plates must be adjusted within the limits specified by the manufacturer or
- The frames must be plumb and level and spaced to adequately support the
- If uplift could cause the components to separate, locking pins must be used and the components Uplift might be caused by the action of wind on a secured deck or by the leverage action of a cantilever side bracket on the scaffold. All joints must be pinned on rolling scaffolds and free-standing towers.
- With a rolling scaffold or free-standing tower, the platform height must not exceed three times its smallest base dimension (3 to 1 rule).
- A scaffold built above the 3 to 1 rule must be effectively guyed or secured to a building or structure to prevent overturning. The guying of a scaffold may require the direction of a professional engineer. Other methods of tying the scaffold should be of a push-and-pull- type mechanism and located no more than 6 m (20 ft.) vertically and 6.4 m (21 ft.) horizontally, after the first tie has been installed to comply with the 3 to 1
- Guardrails must be installed on all open sides of the platform where a person could fall a distance of 3 m (10 ft.) or more. The top rail must be placed 102–112 cm (40–44 in.) above the work surface. An intermediate rail must be placed halfway between the top rail and the toeboard, if one is provided, or halfway between the top rail and the work surface if no toeboard is The guardrail must be able to withstand a load of 550 N
(125 lb.) applied at any point on the top rail.
- Toeboards must be installed on all the open sides of a platform where it is possible for tools and or materials to roll off. The top of the toeboard must be at least 10 cm (4 in.) above the If loose materials are to be stacked above the height of the toeboard, then the toeboard must be increased in height or mesh panels must be installed to prevent materials from falling off the scaffold.
- Ladder access may be vertical or sloping. Ladders must be secured at the point of support and must extend approximately 1 m (3 ) above the landing. A vertical ladder must have a clear space of at least 15 cm (6 in.) behind each rung.
Before erecting access frame scaffolding
- What will the scaffold be used for? For example, light duty (one or two workers; painting a wall), or heavy duty (several tradespersons, with large and heavy materials on the platform)?
- How high will the scaffold be? Will it be erected in one operation or as the work progresses?
- Is the ground firm? Can it support the loads from the scaffold, workers, and materials on it?
- Will the scaffold need to be tied in? How will this be done? Will the ties be moved as the work progresses?
- Is the scaffold likely to be covered or enclosed as a protection against the elements? Is there provision for adding additional ties to the adjoining structure?
- What will be the method of access and egress? For example, a sloping ladder, vertical ladder, built-in stairway, or direct from the floors of the building structure?
- On a multi-level scaffold, how many levels will be loaded with materials at one time? Will an engineer be required to make the calculations for the total anticipated loading and possibly design the scaffold and the sills?
- If a rolling scaffold is required, consider ground surface, height restriction (3 to 1 rule), hazards when moving (such as power lines, projections from the building, and potholes).
Equipment Inspection
You must inspect the equipment you plan to use to make sure that it is in good repair and suitable for the job. Check the following:
- Sills: Suitable size and strength for the loads. Not split or
- Adjustable bases: No thread damage, no curling or warping of the base
- Frames: No cracks in the welded joints. No kinks or dents in the top or bottom cross-members. Legs plumb and square with the cross-members. Brace locks in good working Coupling pins in place and secured to the frame.
- Cross-braces and plan brace (gooser): Straight with no bent Pivot connection in good working order. No excessive rust.
- Planks: No split ends, saw cuts, notches, protruding nails, excessive warping. No contamination that may affect the integrity of the plank, such as oil, chemicals, and burns. (If you have any doubts about the strength of the plank you may need to have it load-tested).
- Plywood decks: Not misshapen or cracked. Locks working. All bolts and screws in No burns or broken ends. If upper surface has non-skid coating, no rot or plywood separation on underside.
- Side or end brackets: Hook-on attachment not distorted. No cracks in welds. No dents, kinks, or any signs of
- Guardrails: Straight, with no kinks, dents, or excessive
- Vertical ladders and brackets: Clamp on bracket is right size and works properly. No cracks in welds on ladder Ladder straight with coupling pins secured.
- Casters: Same size and from same manufacturer. Wheel rotates well and the swivel below the stem is Brake mechanism works properly. Wheel tread has no damage.
- Screw jacks: No cracks in weld where screw jack is attached to the top of the caster. No thread damage. Adjusting nut is a tight
- Other equipment: Inspect any other equipment in the frame
Damaged equipment should be tagged and marked as not fit for use. Inform the supervisor so that others do not use it. If a supplier sends damaged equipment, make sure it is returned. A supplier must ensure that equipment is safe to use